Pattern being readied to add phenolic urethane molding sand, photo of above pattern with internal nylon vents being applied
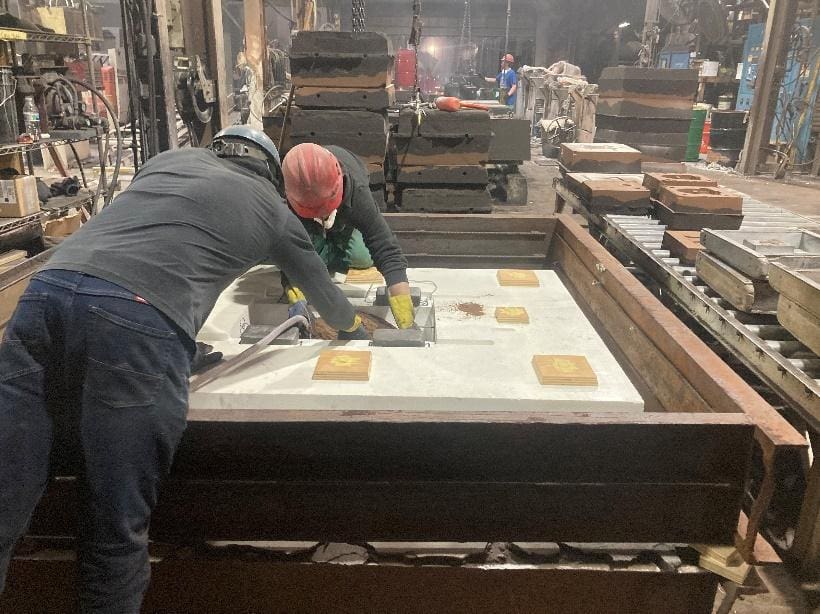
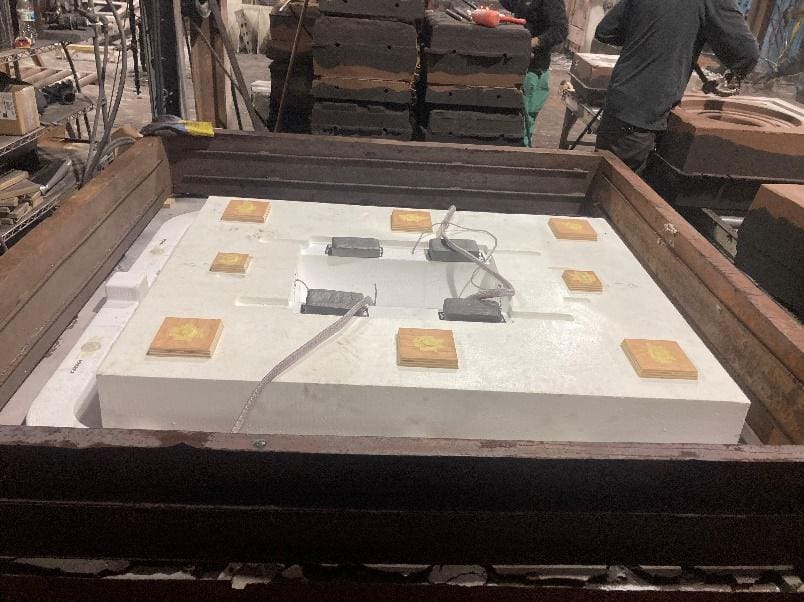
Photo of cope pattern with foundry engineering added–down sprue to deliver metal from ladle to mold cavity. 12” riser sleeves to assure proper feeding of casting once poured. The casting weighs 1,515 lbs., the pour weight is 3,648 lbs.
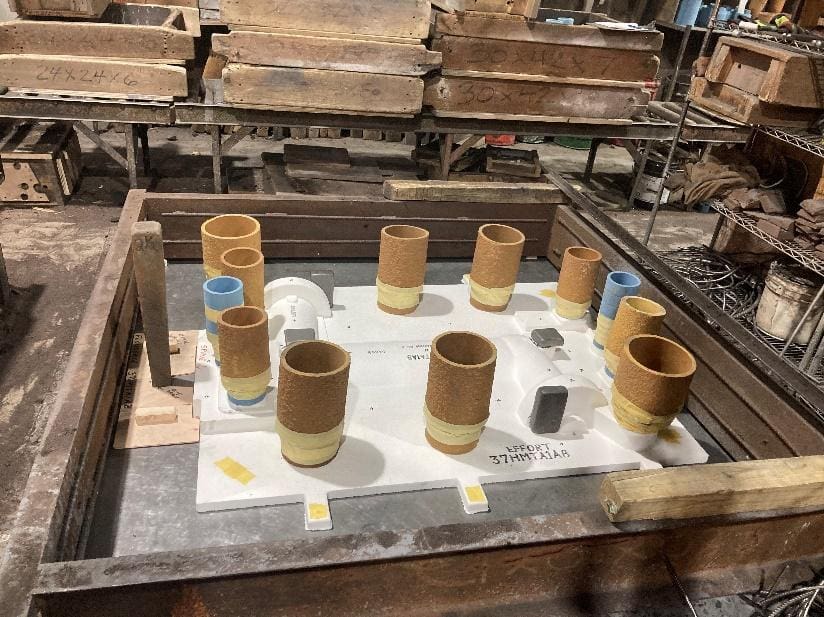
Starting to cover the Styrofoam pattern with phenolic urethane molding sand.
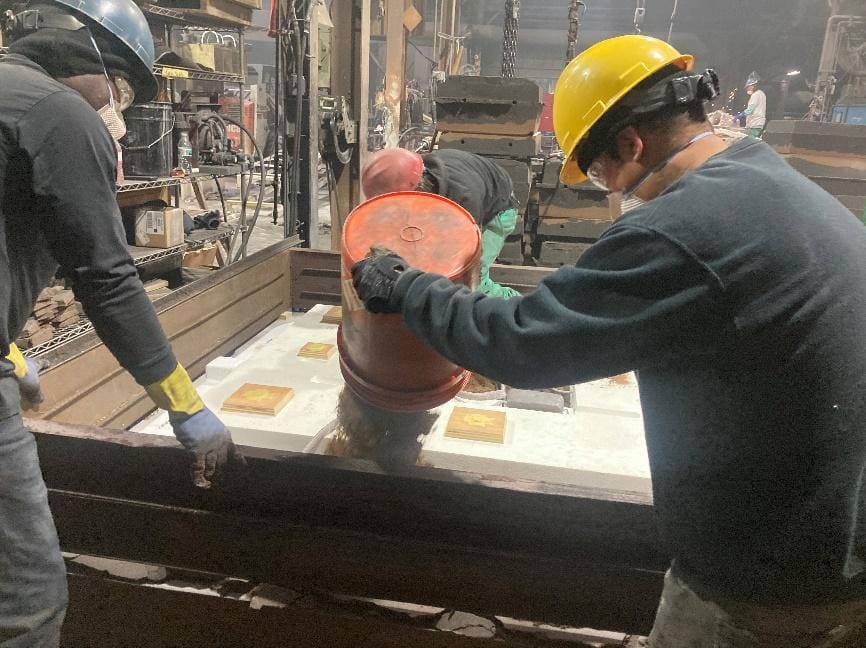
Cope mold is full and being “striked off” to level the cope. The drag (bottom) portion of the mold is made similar to the cope.
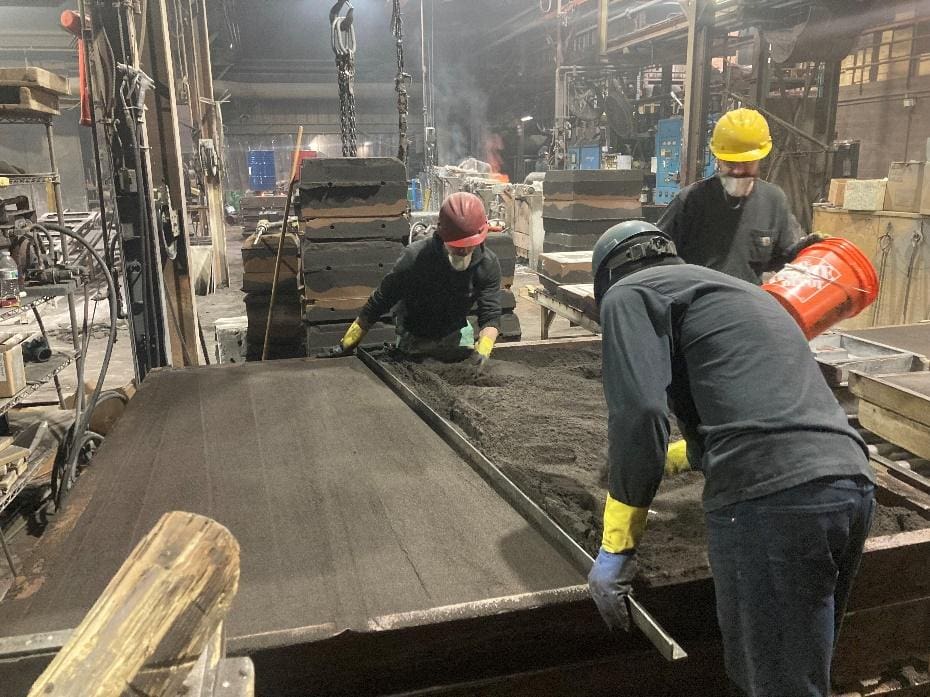
The Styrofoam 1-time use pattern is removed from the mold after the sand hardens. There are 6 draw straps attached to the overhead crane to withdraw the Styrofoam pattern.
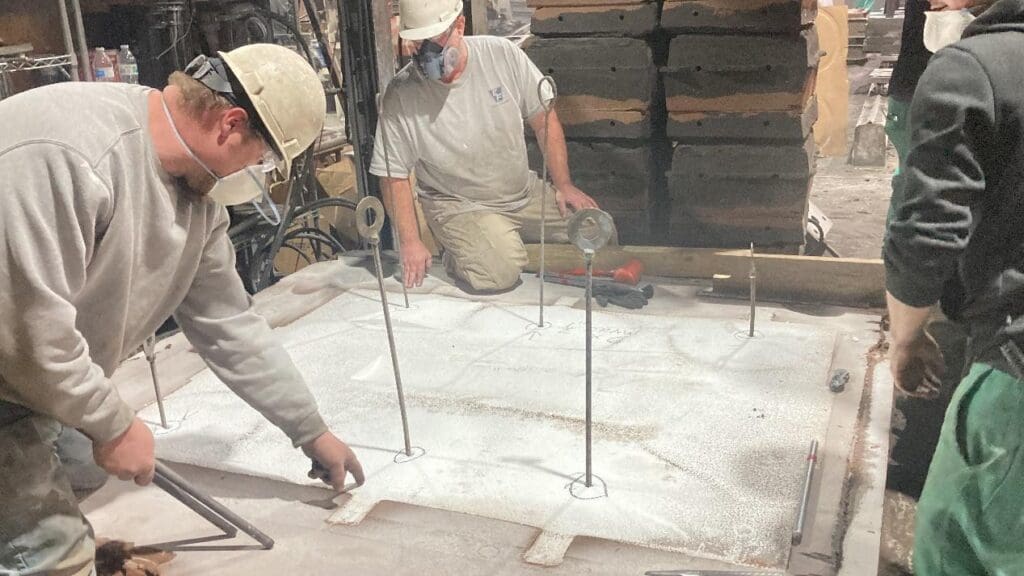
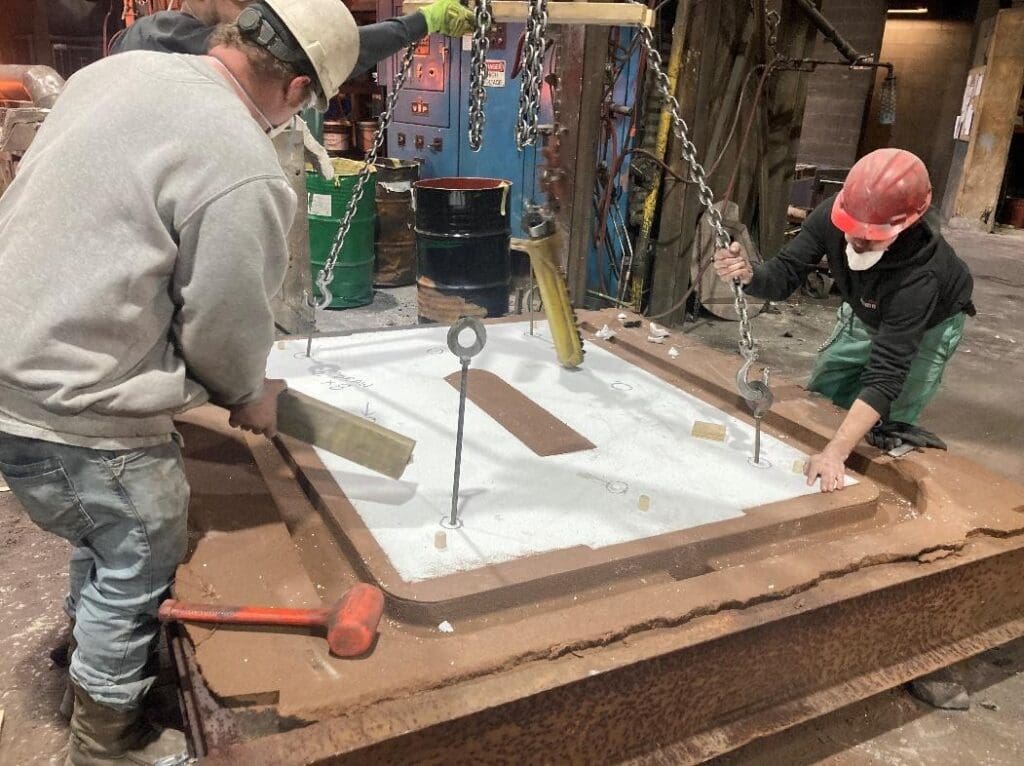
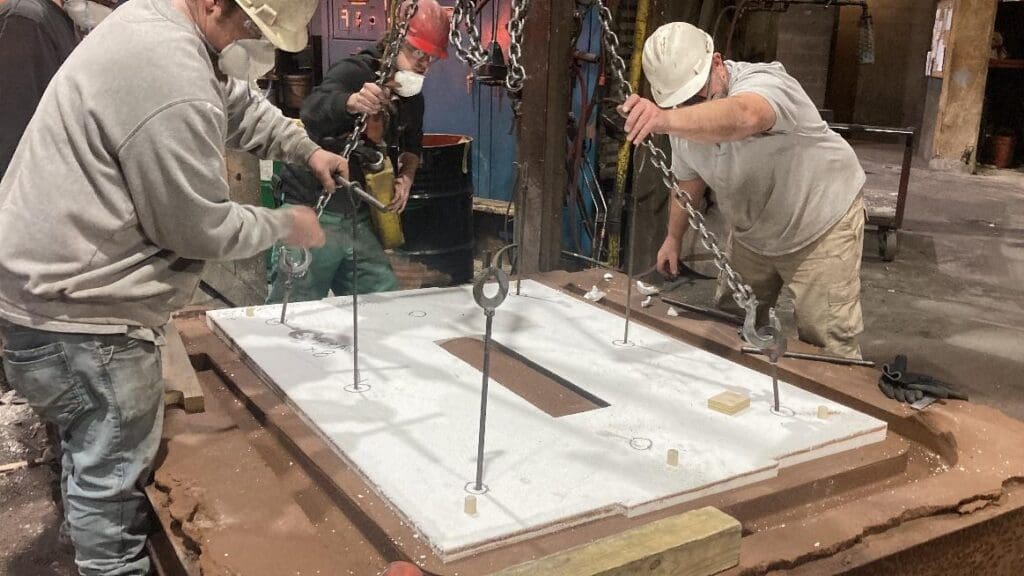
Photo of mold with Styrofoam pattern removed
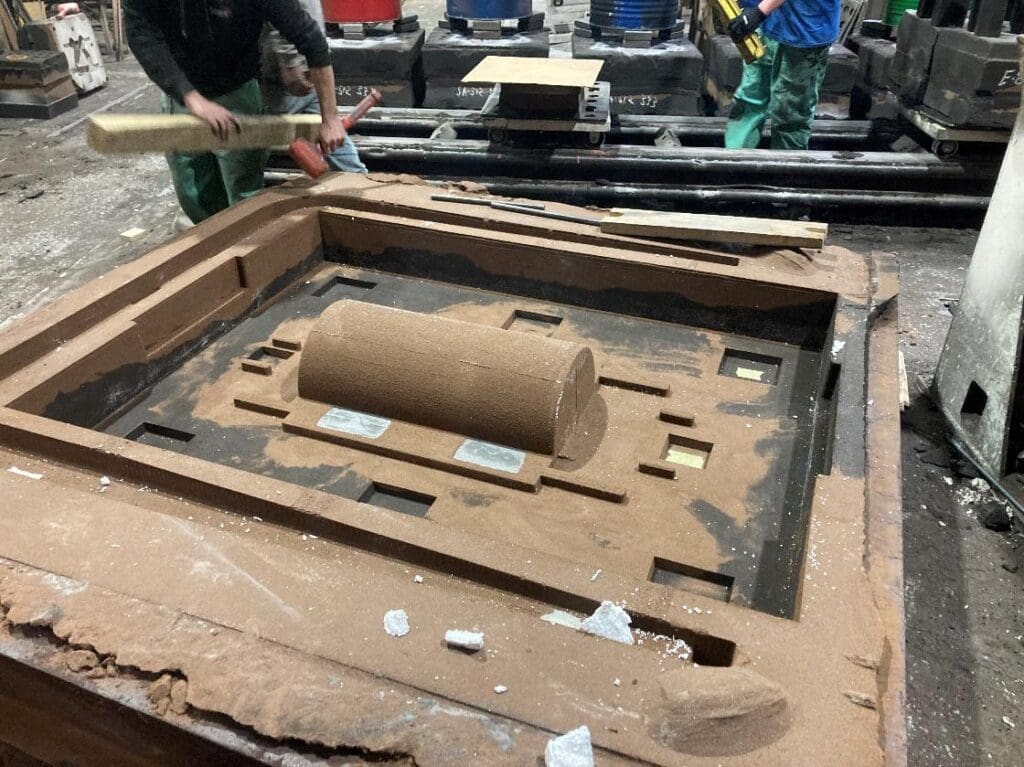
The mold is coated with a 3-4 mil coating to improve surface finish of cast part.
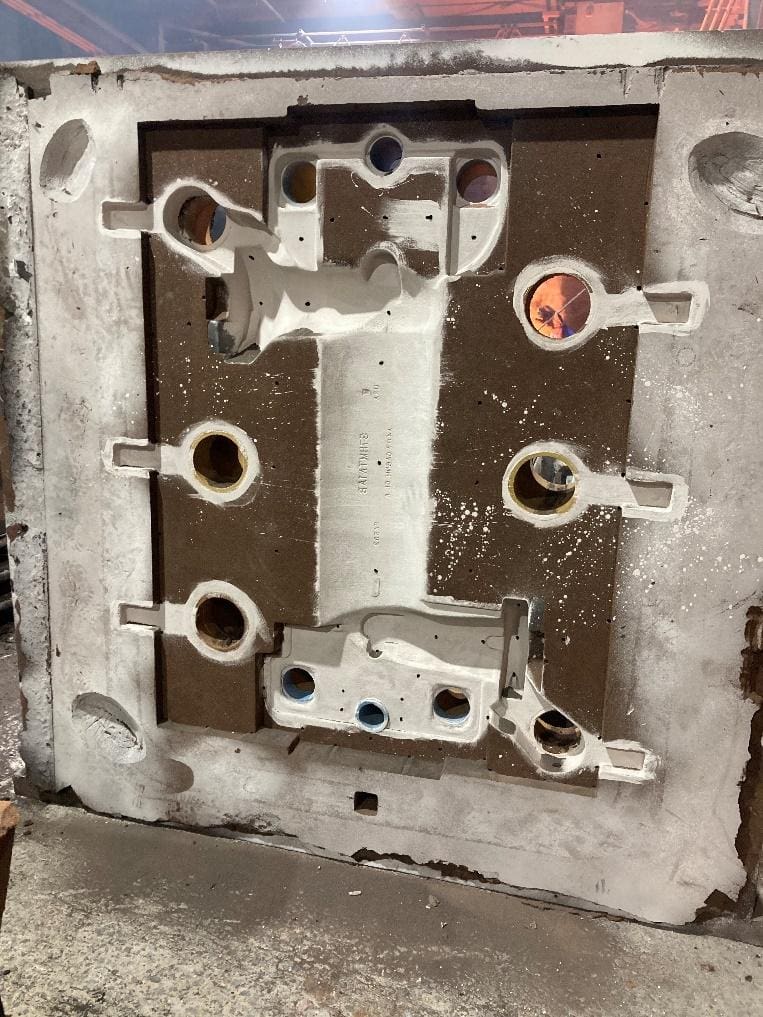
Photo of printed cores coated and ready to place in mold.
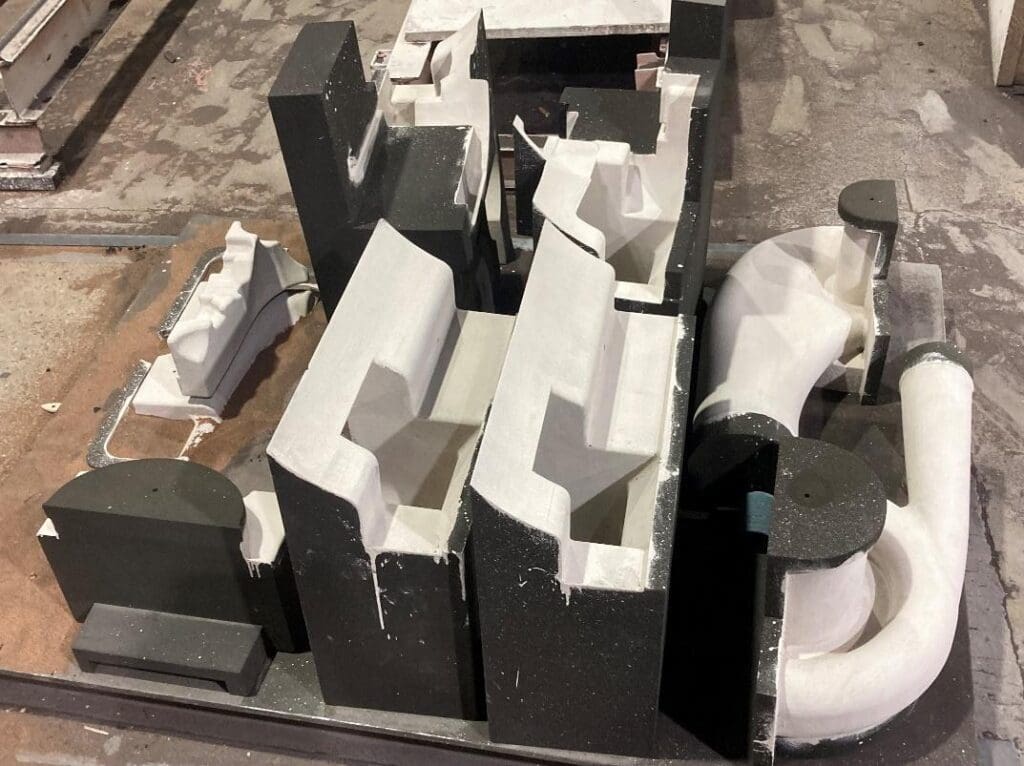
Photo of printed cores placed in drag.
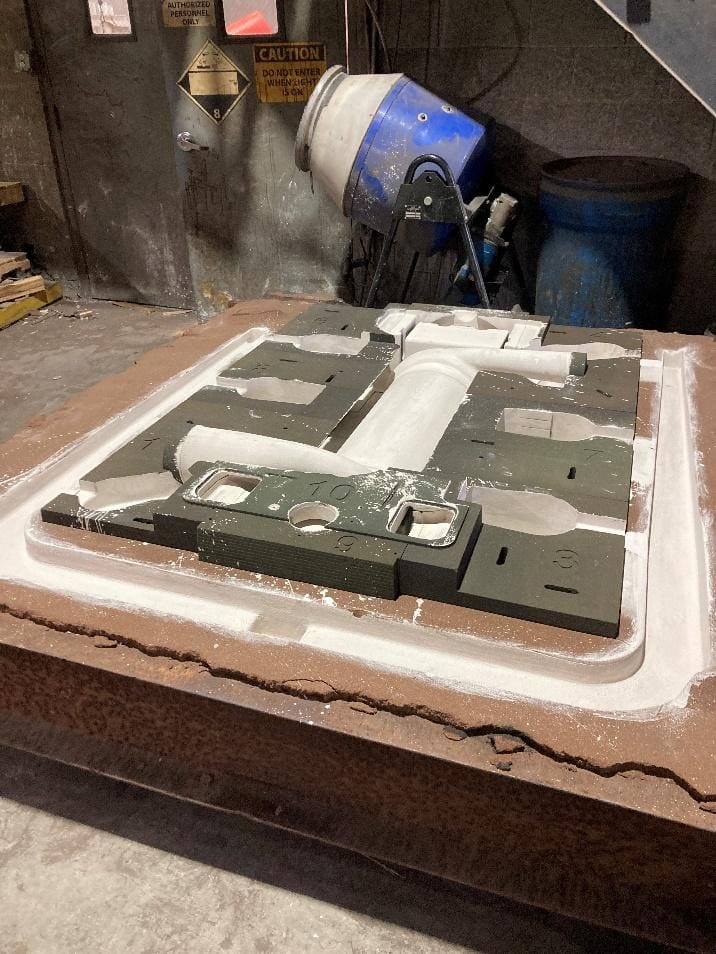
Photos of casting the part with ASTM A216 WCB metal the drums on top are loaded with steel to assure the cope (top) and drag (bottom) stay tightly together. Pouring temperature is 2,825 degrees.
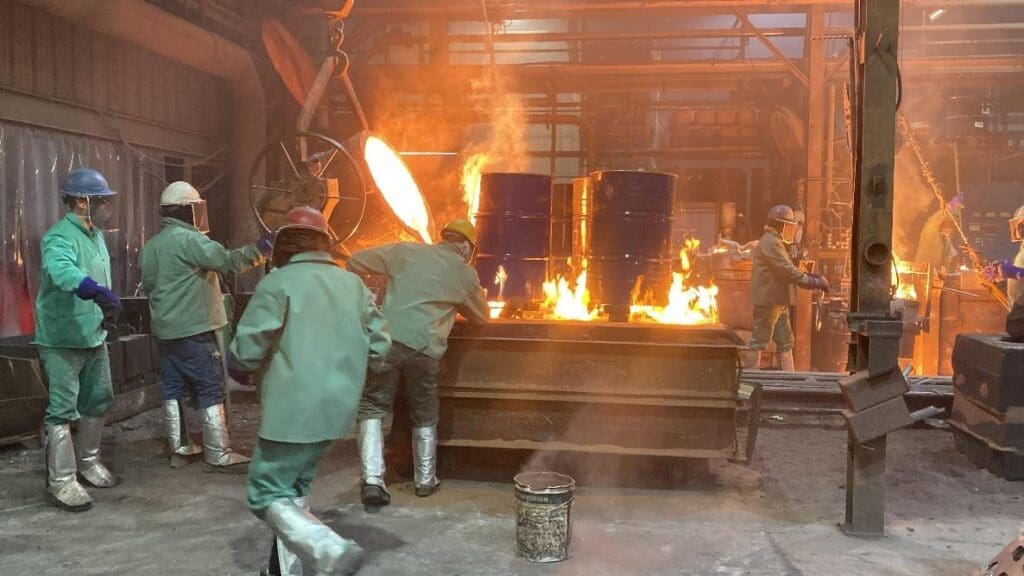
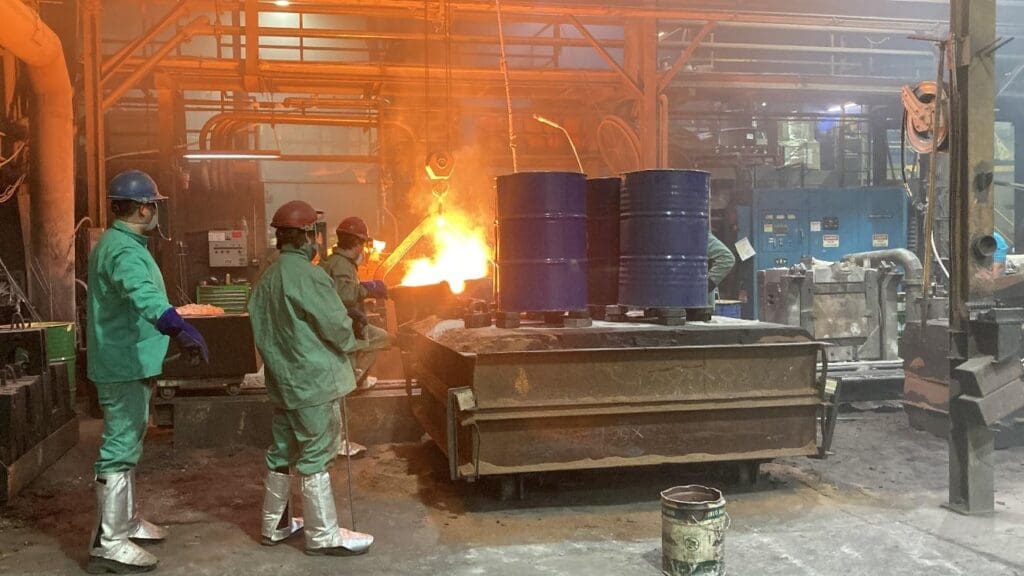
Photo of casting with all rigging removed and available for inspection and upgrading.
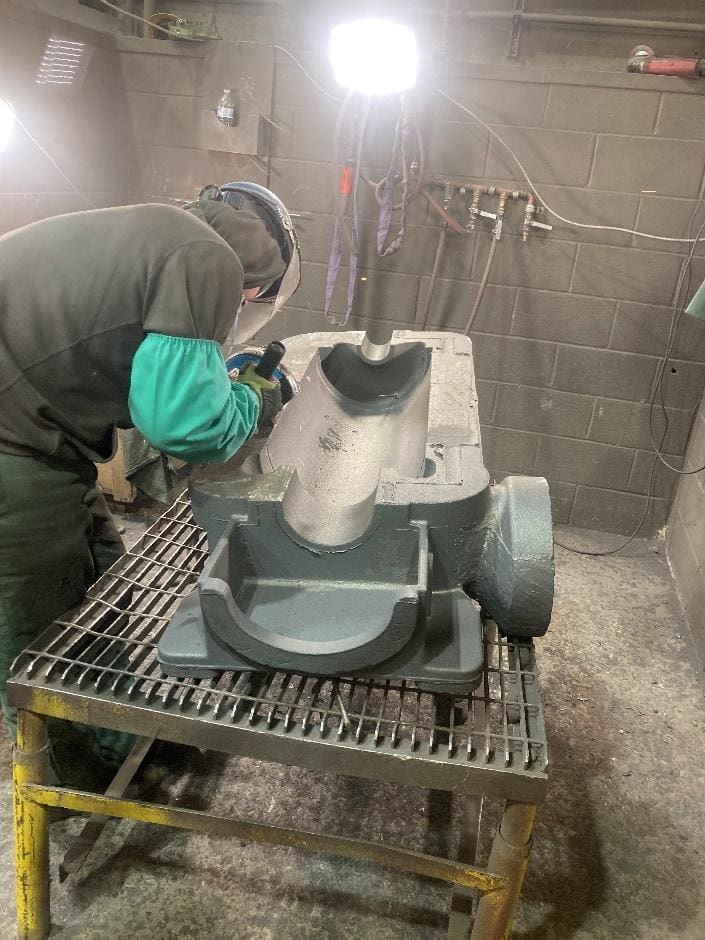
Photos of casting ready to ship.
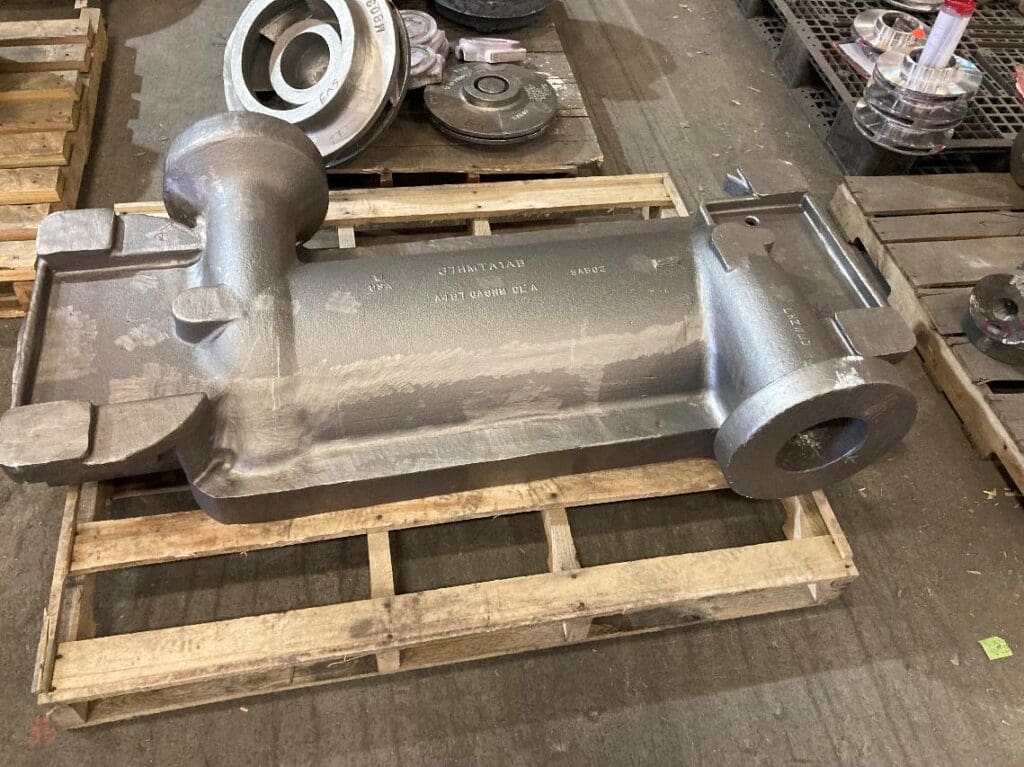
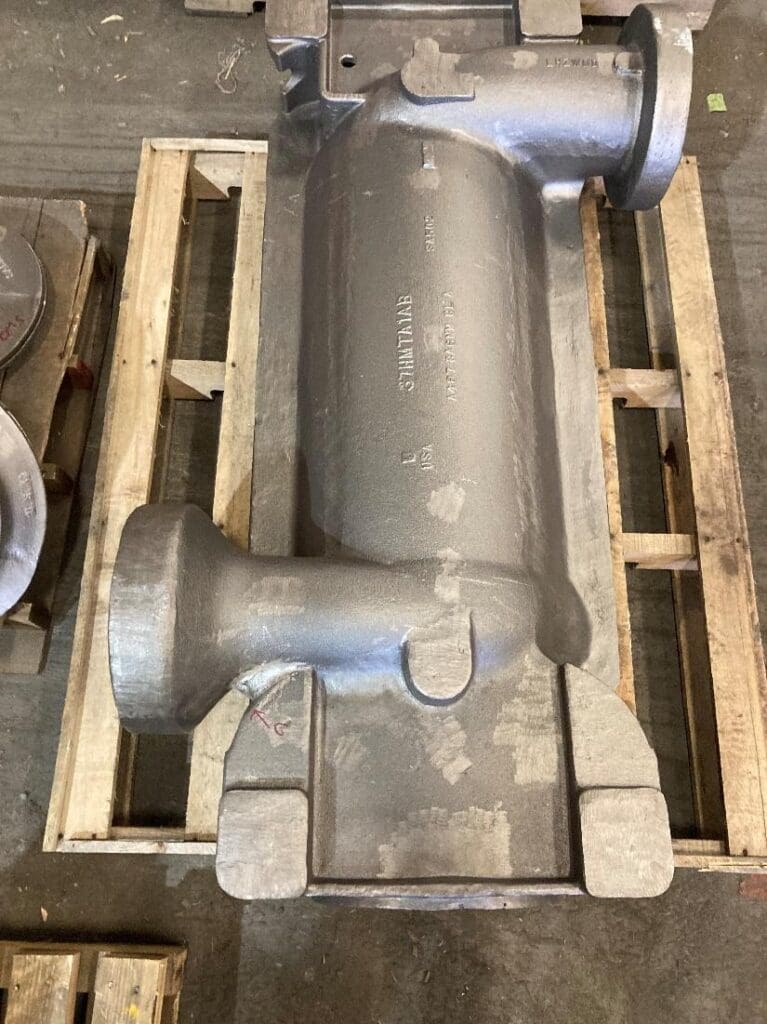