Capabilities
With over a century of experience between them, Director of Quality Assurance Maynard Gross and President William Easterly are the undisputed Masters of Melting.
Their experience spans metals from carbon steel to nickel base, including Monel™ copper-nickel, and all stainless steels. Their expertise extends to Super Duplex Stainless Steels such as CE3MN, CD3MN, CE8MN, CK3MCuN, and Hastelloys (CCW12MU, CW6M, CW2M, CW2MW, and CX2M).
60% of all orders are one piece. Effort Foundry specializes in single-piece orders, usually castings that are large and even complex.
With so much knowledge and experience on staff, Effort is your foundry of choice for melting and pouring all of the difficult alloys.
If it melts, we pour it!
From one pound to one ton, Effort castings are engineered to meet a range of specs and are produced to satisfy our customers’ most exacting requirements.
Specifications
ASTM | AISI |
DIN | SAE |
Military | ARR |
ASME | Customer-specific |
Effort’s experienced foundrymen, ASME/Military accredited welders, and other production professionals have vast experience with a number of alloys:
Alloys
Carbon Steel | Iconel® | Iron | Monel |
Cu-Ni | Austenitic-, Ferritic-, Martenistic-, and Duplex Stainless Steel | Heat-Resistant | Low Alloy Steel |
Manganese Steel | Aluminum Bronze | Nickel Aluminum Bronze | Ultimet |
Sampling of Cast Alloys
ASTM A 128 Manganese | A48 CL 25 to CL 50 Iron | 150-125 | 90-60 | CA40 | CD3MN | CD4MCuN | CE8MN |
CF3MN | CD4MCuN | CE8MN | CF3MN | CG3MN | CK3MCuN | CW12MW | CW6MC |
CY40 | GX3CrNi13-4 | HN | HX | LC2 | LCC | M35-2 | WC1 |
WCA | 105-85 | 70-30 Cu0Ni | A 536 Ductile Iron | CA6NM | CD3MWCuN | CD6MN | CF3 |
CF8C | CG8M | CN3MN | CW2M | CX2MV | CZ100 | HH | HT |
Iconel 601 | LC3 | M30C | N12MV | WC6 | WCB | 120-95 | 80-50 |
CA5 | CB7Cu1 | CD4MCu | CE3MN | CF3M | CF8M | CH10 | CN7M |
CW6M | CX2MW | Ductile Ni-Resist Type 1 | HK | HU | Iconel 625 | LCB | M35-1 |
N7M | WC9 | WCC |
Effort’s in-house heat-treat facilities include furnaces measuring up to 56” x 92” x 42”, suitable for normalizing and tempering any of our alloys. All furnaces are computer-controlled, calibrated, and surveyed to ASME Military standards and nuclear standards.
The new heat treat for all normalization and tempering of carbon, low alloy and martensitic steels has a Nitrogen-enriched atmosphere during all cycles.
The Nitrogen-enriched atmosphere reduces Oxygen present — this drastically reduces oxidation of the castings (scale formation). The end result is much cleaner casting surfaces with little or no oxidation (scale).
Our Fast Track option offers immediate response with deliveries as quick as one week, as needed by the customer.
Other services available include rough- and final machining, passivation, painting, radiography, electroplating, and electropolishing. Together with our in-house capabilities, these services — provided by ISO 9001-approved vendors — make Effort Foundry a true single-source supplier.
Machining Capabilities
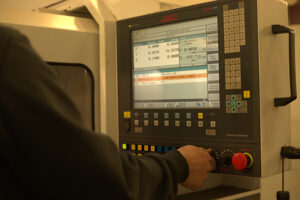
Vertical Milling:
Milling, drilling, and tapping–Fryer MC-10 CNC Vertical Mill – Siemens 840D control
- 30” x 18” x 22” (XYZ) working area
- 25hp – 8000rpm CAT40 taper spindle with 20-tool carousel
Vertical Turning:
Turning, drilling, and tapping; milling on top and sides–Fryer VT-40 CNC Vertical Lathe – Siemens 840D control
- 40” swing – 38” Stroke
- 40hp – 1000rpm spindle
- 8-station live tool turret
Horizontal Turning:
Turning, drilling, and tapping; milling on front/sides–Fryer ET-40 CNC Horizontal Lathe – Siemens 840D control
- 40” swing – 60” between centers
- 30hp – 1000rpm spindle
- 12-station live tool turret
Horizontal Milling:
Milling, drilling, tapping, with machining on 5 sides in one holding and two rotary devices with full 5-axis capabilities–Fryer HR-40 CNC Horizontal Mill – Siemens 840D control
- 40” x 30” x 25” (XYZ) working area
- 4th and 5th rotary axis
- 40hp – 6000rpm CAT50 taper spindle with 30-tool carousel
Keyway Cutter:
–Davis Model 15 Keyseater
- 1/16” to 1-1/2” wide by 12” long keyway cutter
Additional Equipment/Software:
–Faro Edge Measuring Arm
- 9 ft (2.7m), 7 Axis
- Laser Line High Definition Laser Scanner
–Solidworks 2015
- 3 seats
–Esprit 2015 CAM
- 3-axis turning and 5-axis milling toolpath creation
–Geomagic Design X
- Reverse engineering software by 3D scan data processing for FARO Arm
–FARO CAM2 Smartinspect
- Solution for measuring basic geometry and dimensions including 3Dview for FARO Arm