The crew that takes the first step in converting the pattern to a casting is our molding department.
The crew consists of Cory Cesanek, Jeff Gruber, Tylor Hopkins, Corey Wendell, and Adam Yenca.
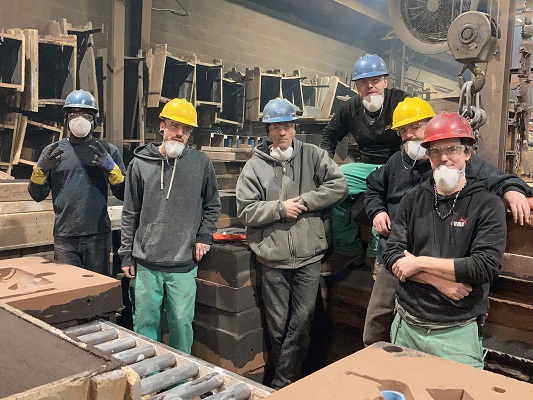
“Set-up” to prepare pattern for filling with phenolic urethane bonded sand, this includes following the engineering instructions to put, chills, tile gating, and riser sleeves on the pattern prior to molding.
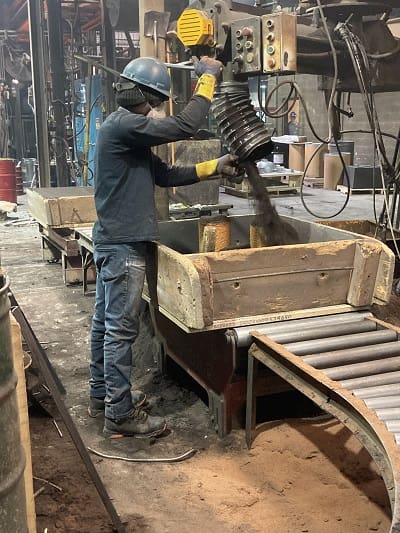
“Mixer Operator” is the person assigned with filling the pre-setup pattern with the bonded sand. Sand is delivered through 2 – 250#/min high-speed auger mixers while air-injecting 1% binder to coat sand.
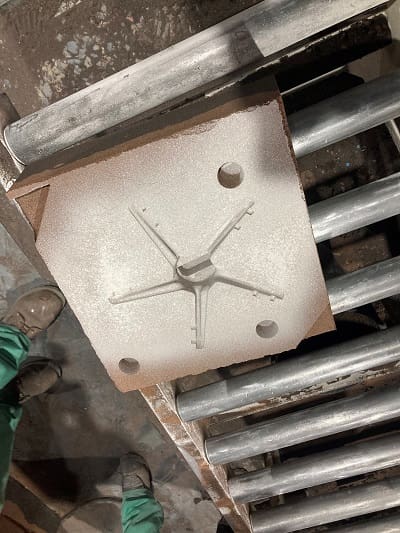
“Knockout Personnel” After waiting for sand to harden (10-20 minutes), the bonded sand mold halves (cope/drag) are separated from the pattern. Each mold half (cope/drag) is washed (sprayed or brushed) with an alcohol refractory coating to enhance the cast finish.
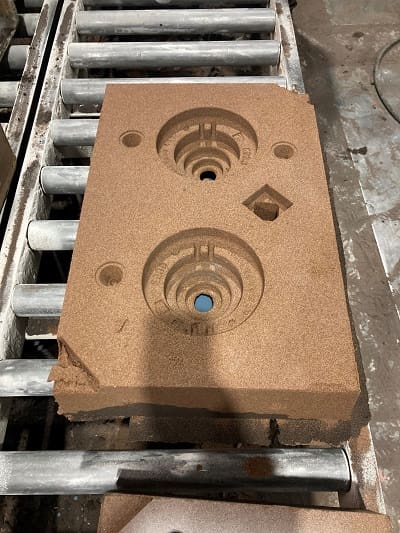
The leader Cory and his crew are responsible for achieving the mold schedule daily from 30 to 50 molds a day depending on the mold sizes. Mold sizes can range from 12” x 12” to 72” x 72”.