Effort Foundry’s Lean Initiative
Lean manufacturing is a philosophy that, in basic terms, is used to reduce waste in manufacturing, resulting in greater efficiency and more value for the customer. An efficient factory will have higher production capability and make products with a lower defect rate.
The Lean system is based on their “5S” method: “Sort”, “Straighten”, “Shine”, “Standardize” and “Sustain.” Typically, a Lean team is staffed to implement and sustain the program.
The Effort Foundry Lean Team consists of
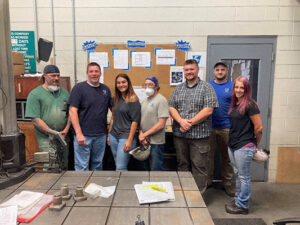
Effort Foundry Lean Team
- Heather Shuster, Manager of QC
- Dylan Apple, QC Technician
- Christian Morganstern, Foundry Manager
- Danielle Steiner, Sales Manager
- Charles Holland, Foundry Supervisor
- Dennis Fritzinger, Finishing Room Supervisor
- Kyle Hamburg, Facilities Manager
- Tanner Apple, Leader, Maintenance Department
The Lean Team has been working on the “5S” method the last 8 weeks, and has accomplished an amazing amount of Lean initiatives —
Six Lean Info Boards have been posted throughout the shop, giving daily results for production, shipments, bookings, quality issues, and mission statements, as well as department-related news.
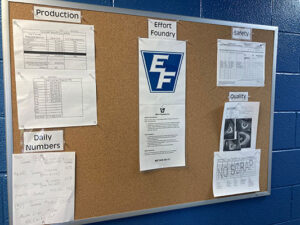
Effort Foundry Lean Info Board
East Side upgrading / Heat Treat has reduced clutter and installed shelving in several locations to improve production flow, identification of product, and staging of work.
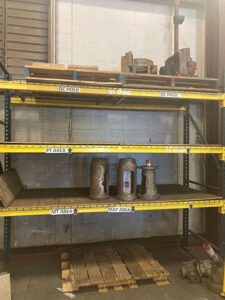
Effort Foundry Lean Shelving
Drawings of the floor space are in process for warehouse, East Side floor space, foundry warehouse, and storage, to aid in implementing improved storage and production flow.
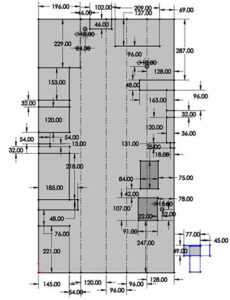
Effort Foundry Lean Floor Space Drawing
Areas were cleared out in the foundry to label and store all raw materials for the proprietary ceramic core process.
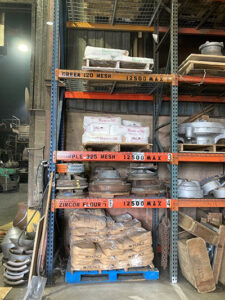
Effort Foundry Raw Material Storage
Storage was made available for all direct-printed molds and cores as received to reduce breakage.
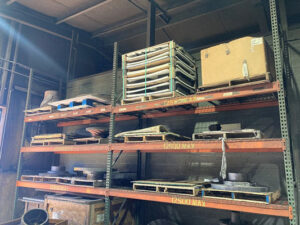
Effort Foundry Mold and Core Storage
These are just a few of the exciting Lean projects. The team will continue to work on the 5S method to make Effort Foundry a Lean casting machine.